I had to put things on hold for a bit due to work, and waiting for other various parts to arrived.
BUT... First flight (for me) has been achieved! 9/1/2018!!
Recap, this is based off the Thingiverse T4 3D-printed body design. It is approximately a "450" class quad. The T4 (to me) is identified by a "guitar" style body that is symmetric left to right, but not-symmetric front to back. The back arms are more angled than the front. The only advantage I see of the arms not being in a traditional true X configuration is that you get a wider field of view in the front (i.e. without the props getting in the camera FOV).
I'd like to thank the person who originally recommended the EagleTree Vector, it has worked out great. While wiring is a bit of a chore, it was fun having my daughter help me with some of the soldering.
I did order a MicroVector (the smaller version of the regular Vector), but decided to not use it (I may use it for my next T4 build). Turns out the regular Vector works so well, I don't want to bother rewiring things.
I've swapped to different motors and ESC, as described below.
**************************************************************************
So, here is a "
2018 Parts Guide" for the T4 Quad that I used to get this thing off the ground with OSD video feed: (search these by name on amazon.com)
- 4x Turnigy D2836/11 750KV Brushless Outrunner Motor
NOTE: I actually ordered 6 of these, since I broke the wires on one of them (literally tugged them out of the motor housing, so be gentle with those!). They came from different vendors and what I eventually noticed is that the motor shaft is longer on some of them, or the metal collar they use to mount the propeller is slightly different between builds (resulting in different heights of where the propeller sits). This concerns me as far as repeatability, so something to watch out for. Also note that these come with short cables (like 4 inches) using mini-bullet connectors. To reach down the arm of the T4, these wires need to be extended.
- 4x 30A RC Brushless Motor Electric Speed Controller ESC 3A UBEC with XT60 & 3.5mm bullet plugs
NOTE: The first set of Castle ESC's I tried were used and maybe had some sync problems. All I can say is these "RC" ESC's worked flawlessly. They include mini-bullet connectors, so they match the motors in that regard. My issue is that the wires on both ends of this ESC are longer than necessary (like over 2X as long as they need to be). Since you're always going to have an extension or intermediate wire between the motors and the ESC, why not just let the ESC wires be as short as possible? This is just a nit note to the vendor of ESC's in general. Be prepared to chop wires and slice/solider extensions.
- 2x XSD MOEDL 12 PCS 300mm Motor to RC speed controller ESC Extension Cable with 3.5mm Bullet Connectors
alternate: Homyl 4.0mm/3.5mm Gold Bullet Banana RC Brushless Motor ESC Extension Cable Wire
NOTE: These are the mini-bullet extension cable I used between the motors and ESC. They are stated as 300mm long, and I estimate them being about 3 inches longer than needed. The alternate described probably would have been better (but still need to order 2x copies).
- TecUnite 20 Pieces 3-Pin Extension Cable Cord Female to Male Lead Wire Connectors for Servo Extension Connection Control Board Remote Control Parts(4 Sizes)
NOTE: I actually got an alternate to this locally at a Hobby Store (3-pin extension cable). These are needed between the EagleTree Vector pins and the ESC's (and have to drop thru the body of the quad). 4 inch might work, 6 inch to be safe.
EDIT: If adding top body cover and larger landing gear, I now recommend going with 4S 4500mah 50C instead.
- HRB 3S 11.1V 6000mAh 50C RC LiPo Battery Pack with XT60 plug For RC Helicopter RC Airplane RC Hobby
optional: Fireproof Explosion proof Lipo Battery Safe Bag(7.28″x3.3″x2.5″) with 2 Packs of LiPo Voltage Checker + Warning Buzzer
optional: Tenergy TB6-B Balance Charger Discharger 1S-6S Digital Battery Pack Charger for NiMH/NiCD/Li-PO/Li-Fe Packs w/ LCD Display Hobby Battery Charger w/ Tamiya/JST/EC3/HiTec/Deans Connectors + Power Supply
NOTE: A "fireproof" container to hold a Lipo battery is up to you. In this case, I also wanted the Warning Buzzers. The interesting thing about this particular Tenergy charger is that it comes with an interesting wiring hardness. My local Hobby Store had a similar wiring harness for sales seperately (~$10), which is what I ended up using. Basically by cutting the misc. power connectors on the harness and just soldering back in XT60 connectors (listed below), you can make this harness work as a power connector to the ESC's via the EagleTree Vector Current Sensor (or Battery Adapter).
EDIT: (update) XT60 connectors help for starters, but rather recommend avoid them (too bulky) and using more direct wiring. A single external XT60 connector for the main battery is fine (but not internal for the ESCs).
- Amass XT60+ Male and Female Connector Plug Set for Battery, ESC, and Charge Lead 10 Pairs
NOTE: Used these on the "wiring harness" to make it work with the ESC's. These are larger connectors and not ideal for the size of this quad, but they work well and make it easier to swap out ESC's as needed in the future.
EDIT: (update) Again, I now recommend avoiding XT60 connectors for the internal ESC's.
- Fat Shark FSV1204 - 700TVL CMOS Fixed Mount FPV Camera
NOTE: This becomes the "eye" of the quad. Not the best resolution, but it worked "out of the box" with both the EagleTree Vector and the EMACHINE EV800D (listed below). It's not clear in the specs, but I later realized this is a 4:3 output instead of widescreen. Still, I can report this item integrates and works fine.
EDIT: No plans to do Acro/Angle mode for this class/size, so widescreen may have been preferred.
- ImmersionRC 600MW 5.8 GHz A/V Transmitter
- 5.8GHz Fatshark spiroNET Antenna Set Cloverleaf and SPW - FPV 5.8 - ImmersionRC
- SMA Male to Female Right Angle 90-Degree Adapter Gold Plated Contacts Pack of 2
NOTE: Solid antenna and a great video transmitter (easy to follow instructions). Haven't tried the Microphone/Audio pass-thru yet (little confusion on my part since Vector seems to be mono-only while the ImmersionRC supports R/L stereo). Not sure why it comes with 2, I only needed 1; I'll use the 2nd on another T4 build in the future.
EDIT: (update) Two antenna are included for the vTX transmitter on the quad in the air, and then the video receiver on the ground (so they have matched polarity).
- EACHINE EV800D FPV Goggles with DVR 5.8G 40CH 5 Inch 800x480 Diversity Video Headset Build in Battery
NOTE: I tried to find a USB adapter to allow my laptop to receive these kinds of video signals, but it didn't work. The EV800D worked out great, since we can dissemble the head-gear parts and use it as a regular standalone screen. And the EagleTree Vector OSD overlay displays fine.
- FrSky Taranis X9D plus 16-channel 2.4ghz ACCST Radio Transmitter (mode 2)with X8R
NOTE: the X8R might be a tad over-kill, but I do have thoughts of expanding into remotely controlled lights, or a cargo drop option. The X9D transmitter is very nice, just a tad intimidating on the setup.
- Eagle Tree Vector FPV Controller with Color OSD (XT60)
optional: Vector Cable Set
NOTE: I ordered the extra cable just in case, but not really needed since the Vector kit I ordered already included one.
- Eagle Tree InfoPanel
NOTE: This is kind of an optional part. It has helped us realize some basic user problems.
- Nyloc Nuts & Washers Zinc Plated M3 Forge Pack 60
- TOOGOO(R) M3x40mm 0.5mm Pitch Bolts Socket Cap Head Hex Key Screws 20pcs
- optional: 100pcs/lot M3(3mm) A2 Stainless Steel Phillips Pan Head Self Tapping Screws DIN7981 (M3 x 10mm)
NOTE: The self tapping screws are for attaching a top housing or a lower covering; I have to print larger version for what I need, so I don't have those attached yet at the top or bottom.
- Lowe's: M3-.5 x 6mm machine screws (philips head)
alternate: M3 x 5mm Hex Socket Head Cap Screws,Pack 100-piece,Stainless Steel,Full Thread,Metric,Knuled Head
**************************************************************************
Now, I did NOT tighten up the wiring, so that part is a bit of a mess (with extra zip ties to secure bulky cabling). But I can confirm: the controller transmitter talked to the EagleTree Vector, the Vector powered the video transmitter, the Ev800D received the video, I was able to arm the motors, and applied enough power to lift everything above the house! (and I could pivot left/right, move in all 4 directions, and land).
BUT, it wasn't a smooth flight and I had to "stay on top" of the controls quite a bit. Specifically it had a tendency to drift "left" despite trim adjustments. Granted, it was a bit windy. The quad did stay level at least, it was just drift issues that I had to compensate for with the controls. But I think most of the trouble was having not really calibrated the compass and other aspects of the flight controller. The main point so far was that there is enough thrust to get this bulk off the ground, and that things are communicating properly.
Next I'll work on the calibrations and tidy up some of the layout.
(I'll try to get the current weight later this weekend). The wiring of the Vector is a little vague and I used printed label stickers to help remind me which wiring goes where (or supports which motor). The Vector video pass-thru and OSD was also a little tricky at first. I may try to prepare some diagrams of the setup.
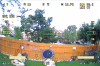