bbodnyk
Active Member
I just finished my complete overhaul of my Cheerson CX-20. While the CX-20 is easy to fly, the downside is it likewise is easy to crash which I have done numerous times necessitating the replacement of the body. Having successfully 3d printed a frame for my Hubsan X4 previously, I decided to design and 3d print a new frame for my Cheerson cx-20; one that would not break.
Fortunately I have at my disposal a Mark One 3d printer manufactured by MarkForged; the only 3d printer capable of placing fiber; fiberglass, Kevlar or carbon fiber, into the layers of the part for strength. Using nylon as the base material along with carbon fiber it is possible to 3d print parts that exceed the weight to strength ratio of aluminum 6061.
The frame is made up of two parts; an upper airframe to which the electronics and motors are fastened to and a lower landing gear section. The two main pieces are spring loaded together to provide about 1/4" of cushioning. Because of the size constraints on the printer bed, the airframe is
made up of 6 individual carbon fiber printed pieces held together mechanically. Likewise the landing gear is made up of a number of pieces with Kevlar being used in the legs. Kevlar is more resilient than carbon fiber which is why it was used there.
I've only flown it a few times but regardless managed to crash it in breezy conditions. I bent one of the aluminum gimbal pieces but no damage to the drone itself. I believe I have achieved my goal which was to design and build a frame that could survive otherwise catastrophic crashes.
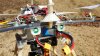
Fortunately I have at my disposal a Mark One 3d printer manufactured by MarkForged; the only 3d printer capable of placing fiber; fiberglass, Kevlar or carbon fiber, into the layers of the part for strength. Using nylon as the base material along with carbon fiber it is possible to 3d print parts that exceed the weight to strength ratio of aluminum 6061.
The frame is made up of two parts; an upper airframe to which the electronics and motors are fastened to and a lower landing gear section. The two main pieces are spring loaded together to provide about 1/4" of cushioning. Because of the size constraints on the printer bed, the airframe is
made up of 6 individual carbon fiber printed pieces held together mechanically. Likewise the landing gear is made up of a number of pieces with Kevlar being used in the legs. Kevlar is more resilient than carbon fiber which is why it was used there.
I've only flown it a few times but regardless managed to crash it in breezy conditions. I bent one of the aluminum gimbal pieces but no damage to the drone itself. I believe I have achieved my goal which was to design and build a frame that could survive otherwise catastrophic crashes.
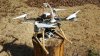
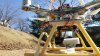
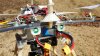