davidhk129
Well-Known Member
I am starting a new 3D print. It's Woverine.
It consists of 13 parts, not including the base.
Cura says I will need 36 hours and 11 minutes to print all of the 13 parts. Based on my past printing experience with my 3D printer, it will take more time than that.
If they come out fine, then it will be a challenge to my painting skill.
Woverine is supposed to look like this...……..
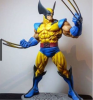
It consists of 13 parts, not including the base.
Cura says I will need 36 hours and 11 minutes to print all of the 13 parts. Based on my past printing experience with my 3D printer, it will take more time than that.
If they come out fine, then it will be a challenge to my painting skill.
Woverine is supposed to look like this...……..
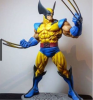